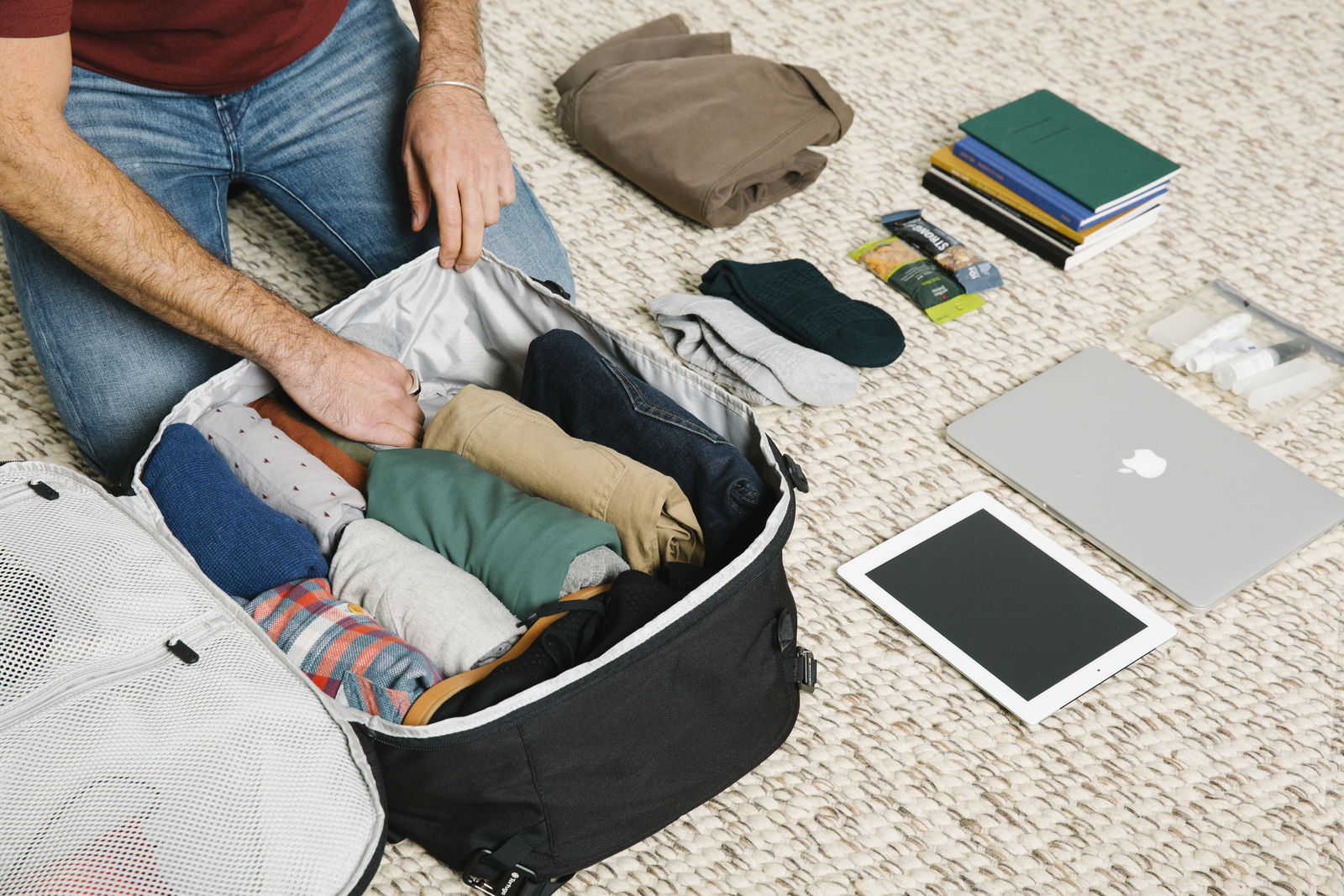
Tortuga Blog
How to Build a Travel Capsule Wardrobe
Steve Jobs wore his trademark black turtleneck. Former President Obama keeps his wardrobe simple to avoid decision fatigue. Forbes even...
READ MORESteve Jobs wore his trademark black turtleneck. Former President Obama keeps his wardrobe simple to avoid decision fatigue. Forbes even...
READ MORE